Metal casting is a process used to create metal components with intricate shapes and details. However, it has become increasingly evident that this activity can have negative environmental impacts due to the toxic fumes released during production and the waste material left over afterward.
In this article, we will explore the effects of metal casting on our environment and discuss ways in which these risks can be mitigated or minimized. We will examine how reducing emissions from production processes, using alternative materials, recycling scrap metals as well and other measures can help reduce pollution associated with metal casting activities. Furthermore, we will consider various techniques for controlling dust particles generated by these operations so that they do not end up polluting our air and water sources.
By understanding these issues better and taking steps to address them, we can ensure a healthier future for us all while still enjoying the benefits of working with metals in manufacturing industries around the world.
The Environmental Impact of Metal Casting
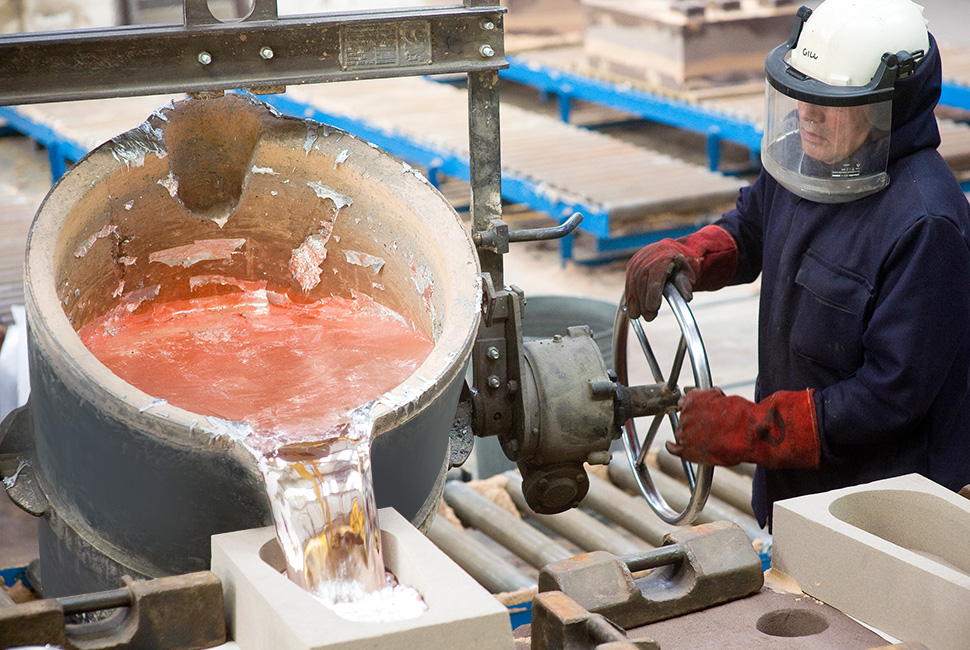
Metal casting is an essential process in many industries, such as automotive and aerospace. However, it can come with environmental consequences, from the use of hazardous chemicals to air emissions.
In this article, we’ll explore the environmental impact of metal casting and ways to minimize it. From a manufacturing standpoint, metal casting techniques involve using heat to melt down metals into liquid so they can be poured into molds that will shape them into desired parts or products.
This process produces various pollutants like smoke and fumes that contain heavy metals such as copper and chromium which are known carcinogens when inhaled over long periods. Additionally, for the molten metal to remain fluid during production runs often requires high levels of energy input which contributes further to air pollution through the burning of fossil fuels such as coal or natural gas.
Furthermore, during the cooling stage after pouring molten metal into molds, there may be acidic vapors released due to chemical reactions between water droplets present in the atmosphere mixing with hot molten metals producing undesirable toxins like sulfuric acid fumes in some cases leading to serious health issues for workers exposed at close range if protective gear isn’t worn properly by the personnel involved in handling these operations. Fortunately, there are ways manufacturers can reduce their environmental impact when engaging in metal casting activities including proper ventilation systems installed near production areas along with other measures such as utilizing robots instead of manual labor where possible while still getting satisfactory results out from cast parts made according to their quality standards required by customers ordering specific items produced via this method as well investing on renewable energy sources (solar panels) whenever feasible cutting down electricity costs associated with running machines used during these processes thus achieving greater efficiency overall from both economic financial savings plus much-needed conservation efforts done towards our planet’s environment simultaneously proving beneficial for everyone involved moving forward on all fronts – businesses owners operators alike!
Ways to Minimize Its Effects
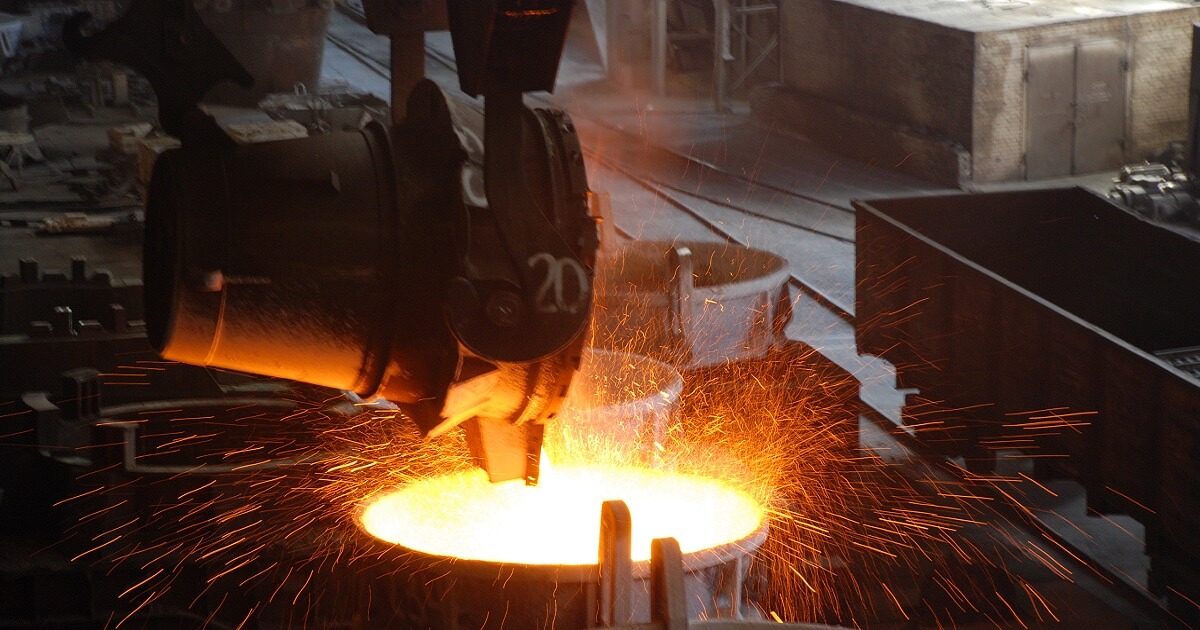
Metal casting has become a popular process in numerous industrial applications, and its environmental impacts can be significant. To help reduce the damage to our planet from metal casting, several steps can be taken.
First of all, companies need to use alternative materials whenever possible. Replacing metals with plastics or wood could significantly cut down on energy consumption during production and lower emissions.
Companies should also research methods for recycling scrap metal from previous projects rather than relying solely on new resources. Another way to reduce the impact of metal casting is by utilizing more efficient techniques when melting metals into their desired shapes.
Using advanced technologies such as induction heating and vacuum casting may result in lower fuel consumption while producing high-quality products that are just as durable as those produced through traditional methods. Finally, proper maintenance of machinery used in metal casting operations is essential for reducing negative environmental effects resulting from excessive energy usage or hazardous chemical releases due to improper handling of equipment components.
Regularly scheduled inspections and replacements will improve safety conditions while ensuring optimal performance levels throughout the entire operation process.
Conclusion

Metal casting is a process used to create metal products, but can have negative environmental impacts. Reducing the emissions of volatile organic compounds and controlling the generation of dust are key ways of minimizing their environmental impact.
The use of improved ventilation systems, adding scrubbers and filters to exhausts, utilizing low-emission binders in core-making processes, and investing in advanced technologies to reduce energy consumption all help reduce the footprint created by metal casting operations. By reducing these hazards while still achieving desired outcomes from the process, metal casting can be made more sustainable for both businesses and communities alike.